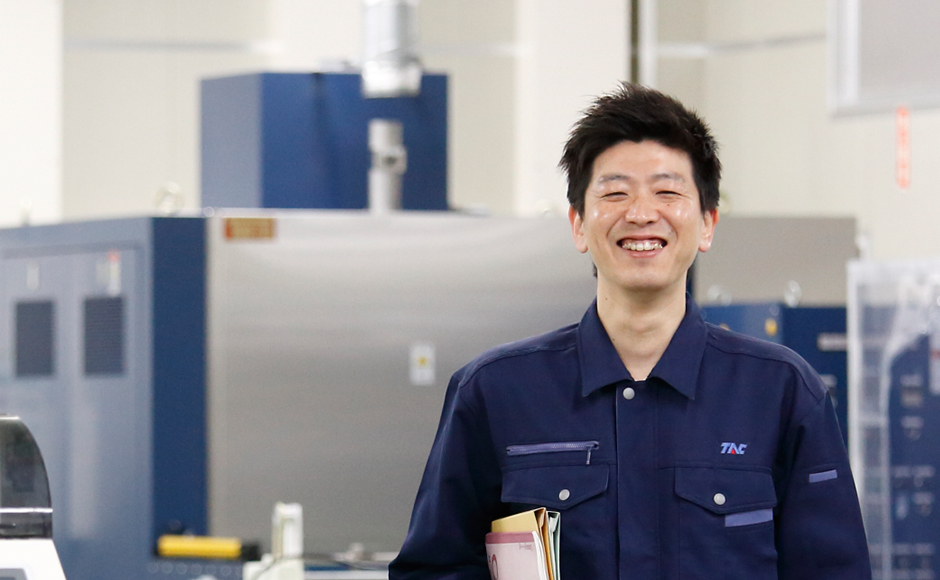
未来づくり最前線
ヒューマンインターフェースの最前線
いち早く研究開発し、
いち早くお客様のハートを掴む
新タック化成株式会社 生産本部山本工場 研究技術部
武藤マネージャー
今や私たちの生活に深く密着したスマートフォンやタブレット。
それらは、指先やタッチペンで操作できる簡易さ、わかりやすさが受けているはず。
そんなヒューマンインターフェース操作は、Windows10以降、中大型のノートパソコンにも普及してきています。
その操作感度は、何も電子デバイスだけで制御されるわけではありません。実は、タッチパネルディスプレイ中に使用される透明粘着シート(以下、OCA※1と略す。)にも、感度を支える技術が詰まっています。
その一端を担う研究最前線をご紹介させていただきます。
注釈※1 OCA=Optical clear adhesive、光学的に透明な両面粘着シート
大型タッチパネルの操作感度を高める低誘電OCA
タッチパネルディスプレイの断面構成と低誘電OCA
タッチパネルの主な動作方式として、指先やタッチペンをタッチパネル表面に近づけると、複数の電極間の静電容量が同時に変化し、電流量の比率を測定することで高精度に位置検出させる静電容量方式があります。
しかし、大面積化すると、位置認識がしにくくなり、タッチパネルの誤作動が多くなってくるため操作感度を良くする機能がOCAにも求められています。その一つが、「比誘電率の低いOCA(以下、低誘電OCAと略す)」です。
低誘電OCAは、液晶モジュールとタッチセンサーモジュールを貼り合せる従来の厳しい品質もクリアーしなければなりません。
ダイレクトボンディング用OCAと呼ばれており、例えば、段差埋まり性(タッチセンサーモジュールの枠縁に黒や白で印刷された凹凸面を粘着シートで埋める機能)、信頼性(高温多湿の環境下でも透明性や見た目が損なわれない機能)、リワーク性(貼り合せ時に時に失敗しても再度剥がしてやり直し易い機能)など、業界標準品質いわゆる「当たり前品質」が目白押しです。
単に比誘電率だけが低いOCAを探し当てるだけではなく、当たり前品質までも全て満たされていなければなりません。多くの評価・検証が待ち構える、ちょっと気が遠くなるような研究のスタートでした。
タッチパネルの視認性向上とストレスフリー化の実現に向けて!
数年前のある日、営業チームと研究開発チームが、ダイレクトボンディング用OCAの未来づくりをテーマに討議するデザインレビュー会議から、事は始まりました。
営業チームは、ヒューマンインターフェースの深化として、タッチパネルが視認性向上で大面積化、さらに、ストレスフリー化でタッチ操作の高感度化が進む次世代動向をキャッチしていました。
研究開発チームは、その動向にマッチした高機能OCAのアイディア出しする中で、電気信号をうまく捉えられる可能性のある低誘電OCAの潜在的ニーズに目をつけました。
開発当初は、どれだけの顧客に低誘電OCAを受入れてもらえるのか半信半疑の部分もありましたが、電子デバイス技術の早い開発スピードに遅れないためにも、そして競合他社よりもいち早く製品を立ち上げて技術力アピールするためにも、最速3ヶ月という期間をくぎって、開発をスタートしました。
効率的開発と徹底したユーザーカスタマイズの両立
研究開発をスタートし、目標となる低誘電化の方向性は早く決まりましたが、問題はダイレクトボンディングに求められる厳しい要求項目の両立でした。
普通の透明フィルムに見えますが、カスタマイズが欠かせません
一つ目の関門は、信頼性。
高温多湿環境でも透明性を維持しなければ、ディスプレイの視認性を損ねてしまいます。低誘電化と信頼性はトレードオフの傾向があったため、幾つもの粘着剤の処方設計を試しました。ときには実験計画法にも取り組み、効率的にゴールを目指し、何とか計画通りに選定ができました。
次なる関門は、段差埋まり性です。
貼り合せるタッチセンサーモジュールには、枠縁に印刷が施されており、その印刷段差が高いほど、OCAで埋めることが難しくなります。そこで、研究所では自作したダミー印刷板を使って初期評価し候補の低誘電OCAをユーザーに提案していきました。
しかし、ユーザーでは、もっと複雑な印刷をしており、その段差形状にも特徴があったため、段差埋まり性が足りない、と厳しいご意見を頂くこともありました。そんなときは、そのユーザーのタッチパネルモジュールで貼り合せる条件を密に試行錯誤する方法が一番の効率よい解決策でした。
ユーザーカスタマイズという意味では、「当たり前品質」のリワーク性も同じです。
ユーザーが貼り合せに失敗したときに、再剥がしをして高価な部材を有効活用することが目的ですが、そのリワーク方法も三者三様ですので、研究者の視点から、リワーク方法のアイデアを各ユーザーに提案することもありました。
実用化へいち早くこぎつけるには、効率的な開発だけではなく、三者三様のユーザーのニーズに徹底的に対応する大切さを痛感しました。
次世代ディスプレイを支えるOCA
気が抜けない毎日ですが、充実しています
競争社会の中で、他社に先駆けて新製品を提案が出来るかが、研究・開発者の使命になると考えています。
いち早く研究開発し、いち早くユーザーのハートを掴むこと。
そこには、研究サイドだけではなく、営業や製造部門の力も一体となって進めなければ成り立たないことも事実です。前述のデザインレビュー会議は、その一体感をもたらしてくれました。
研究開発から量産化までのスケジュールのプレッシャーに、打ち勝ち、打ちのめされの日々の繰返しですが、フレキシブルディスプレイや3次元ディスプレイなど次世代ディスプレイを支えるOCAの研究開発に今後も挑戦し続けます。
“チーム王子” のスピード感あるモノづくり
営業担当とも密に情報交換が必要です
初めての試作品を、目標3ヶ月以内で何とか作り上げ、工場からユーザーへ出荷された日は、感慨深いものがありました。それで終わりではないですが、ひとつの区切りとなる達成感は、それまでの苦労を癒してくれました。
「さあ、ユーザーで評価して頂き、次なる課題に向けて準備だ」、という気持ちでした。
もう一つは、研究所と事業体の新タック化成㈱が同じロケーションにありますので、研究者同士だけのコミュニケーションだけではなく、事業体の製造部とも密接な協力体制があってこそ、納期対応ができたとも言えます。研究開発品を量産品へといち早く纏め上げる“チーム王子”として心強く感じた瞬間です。スピード感あるモノづくりには持って来いのシチュエーションです。
チーム王子、にご期待ください!
下記URLより製品に関する詳細情報をご確認いただけます。
[新タック化成のフィルム塗工]
http://newtack.chips.jp/pdf/kinou_jutaku20150709.pdf
[クリーン設備でのフィルム塗工受託(イプロス)]
https://www.ipros.jp/product/detail/2000421971?hub=59+4485404+31995
[新タック株式会社HP]
http://www.tack.co.jp/
技術・研究に関するお問い合わせ
共同開発などのご相談なども承っております。なんでもお気軽にお問い合わせください。
お電話でのお問い合わせ
新タック化成株式会社
機能製品営業推進部
03-5550-3020
受付時間 9時~17時30分
(土曜・日曜・祝日を除く)